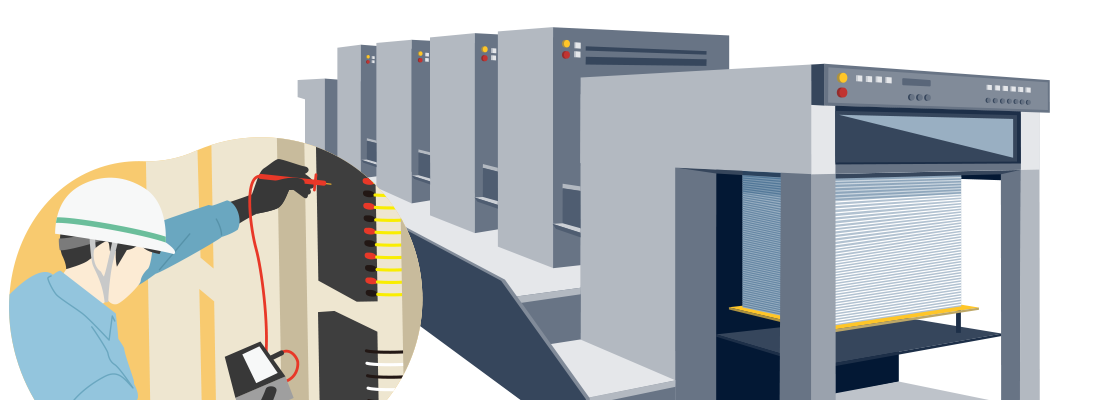
専用マイクの特徴を生かして大型機械の構造部品の歪み・緩みからくる不調データを収集し、予兆分析に利用する事例をご紹介します。
専用マイクの特徴を生かして大型機械の構造部品の歪み・緩みからくる不調データを収集し、予兆分析に利用する事例をご紹介します。
大型の製造機械にはメーカーによる保守メンテナンスを定期的に受けることを保証の前提としている機械が多く、このため機械メーカーでは、保守人員と交換部品を確保し、日々全国各地の顧客拠点を訪問しています。これらの機械を使用して製品を生産しているユーザーにとっても部品交換やグリスアップなどの定期点検は安定した生産活動や安全確保のためにとても重要ですが、一方で、計画停止や保守費用の負担が重いため、本当に必要なタイミングに必要なメンテナンスのみを実施して欲しいという要望が根強くあります。
また、稀にですが定期交換の対象ではない部品が破損したり、外部からの影響で躯体や構造に緩みや歪みなどが蓄積し機械の精度が悪化したり不調に陥ることがあります。このケースの異常は生産ラインの復旧が最優先とされるため故障原因は不明のままになったり、稀なためにデータの蓄積がなく故障個所の特定や交換部品の調達に日数を要したりと、発生頻度は低いものの影響はとても大きい課題です。
メーカーによる保守点検業務には以下のようなニーズがあると考えています。
個体間の違いや経時変化が定量化出来ます
装置の様々な運転モードの音を用いてモデルを作ることにより、運転モードが変化しても正常時からの状態変化を数値化することが可能です。また、基準となる正常音モデルで検査時の音を評価することで、人によらない定量的な評価が可能となり、個体間の差や経時変化も数値化出来るため適切な保守タイミングの判断に用いることが出来ます。
正常音のみでも大丈夫です
現場の装置は、適切にメンテナンスして運用していれば故障することは稀です。故障する前後で装置の音を録音出来れば判定精度は上がりますが、故障が発生するまで録音を常時継続することは現実的ではありません。弊社では教師データなしの機械学習モデルにより音を判別します。この方法は、正常時の音を集め、その音から正常音のモデルを作り、測定した音と正常音モデルが、どの程度異なっているのかを統計的に計算し数値化する方法です。この方法を用いれば、故障時の音を録音することは必須ではありません。
装置から取得したデータを特徴量に変換し、特徴量空間から音の状態値を計算します。特徴量の計算には【FLAC】や【変動音解析】を、状態値の計算には【GMM】や【CNN】を装置特性やニーズによって組み合わせて使用します。計算によって求められた乖離値から閾値を定め正常・異常を判別します。
躯体や構造部品の監視にも対応出来ます
大型装置の音を収集し判断する場合、通常のマイクでは主に駆動音が収集されるため、装置本体の不調を捉えることは困難です。そこで、弊社では接触式マイクを開発しました。これは医者の聴診器のように装置に直接接触させて音を収集するため、部品や躯体に取り付けることで固定ボルトの緩みや歪みなどが原因で構造に伝わる音の変化を捉えることが出来ます。
異音検知をモーター又はモーターを組み込んだ商品の出荷検査業務に適用する事例をご紹介します。
製油所や化学プラントなど、広大な敷地に設置された設備の巡視点検業務に異音検知を活用する取り組みをご紹介します。
風力発電機の遠隔監視に関するニーズや課題に対する取り組みをご紹介します。